Our Machining Capabilities
Solutions. Automation. Precision.
At Rapid CNC Parts.com, our CNC machining operations are built for precision, efficiency, and scalability. We combine 3-axis and 5-axis CNC milling with advanced mill-turn (CNC lathe) technology, industry-leading workholding and fixturing, and collaborative robotic automation. This powerful mix lets us deliver custom parts with exceptional accuracy—at faster lead times and competitive costs.
Whether you’re prototyping a single component or scaling to full production, our capabilities adapt to your needs, ensuring consistent quality from the first part to the thousandth.
Smart Machining with 3- and 5-Axis Systems
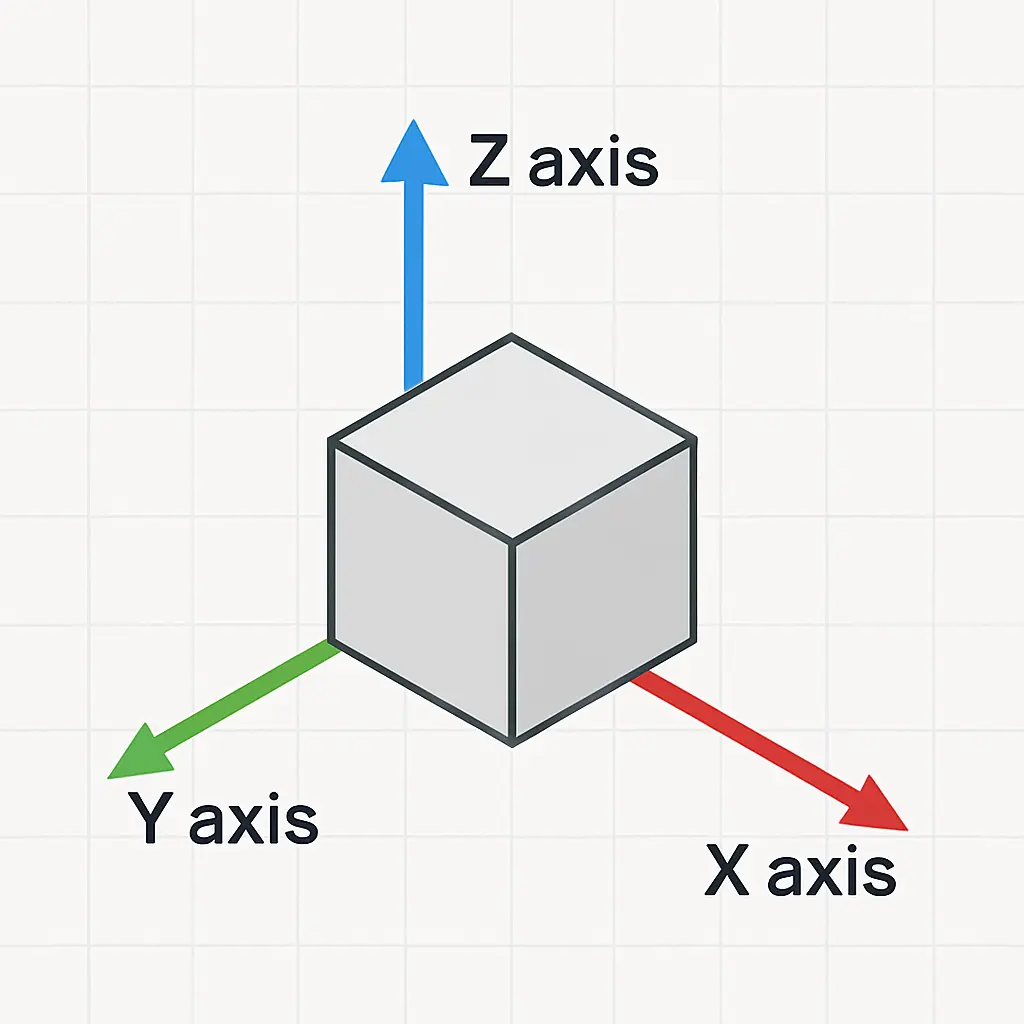
3-Axis Machining
Ideal for prismatic parts, brackets, housings, and plates—our 3-axis CNC machines handle a wide variety of geometries quickly and cost-effectively. With full X, Y, and Z movement, these machines are great for parts requiring pockets, contours, drilled holes, and tapped features with tight tolerances.
Where 3-Axis Shines:
- Cost-Effective Simplicity: Perfect for straightforward parts where most features can be accessed from a single side or require minimal reorientation.
- Fast Setups: Ideal for jobs with tight budgets and lead times.
- Highly Repeatable Production: Great for brackets, covers, plates, housings, and jigs across industries like consumer products, automotive, and industrial machinery.
Typical 3-Axis Applications:
- Precision-milled pockets and slots
- Drilled and tapped hole patterns
- Flat surfaces and contours
- Basic boss and cavity features
Our investment in high-rigidity 3-axis machines (DN Solutions DNM series) and premium tooling enables us to hold tight tolerances, produce excellent surface finishes, and keep cycle times short—even on challenging materials like stainless steel or engineered plastics.
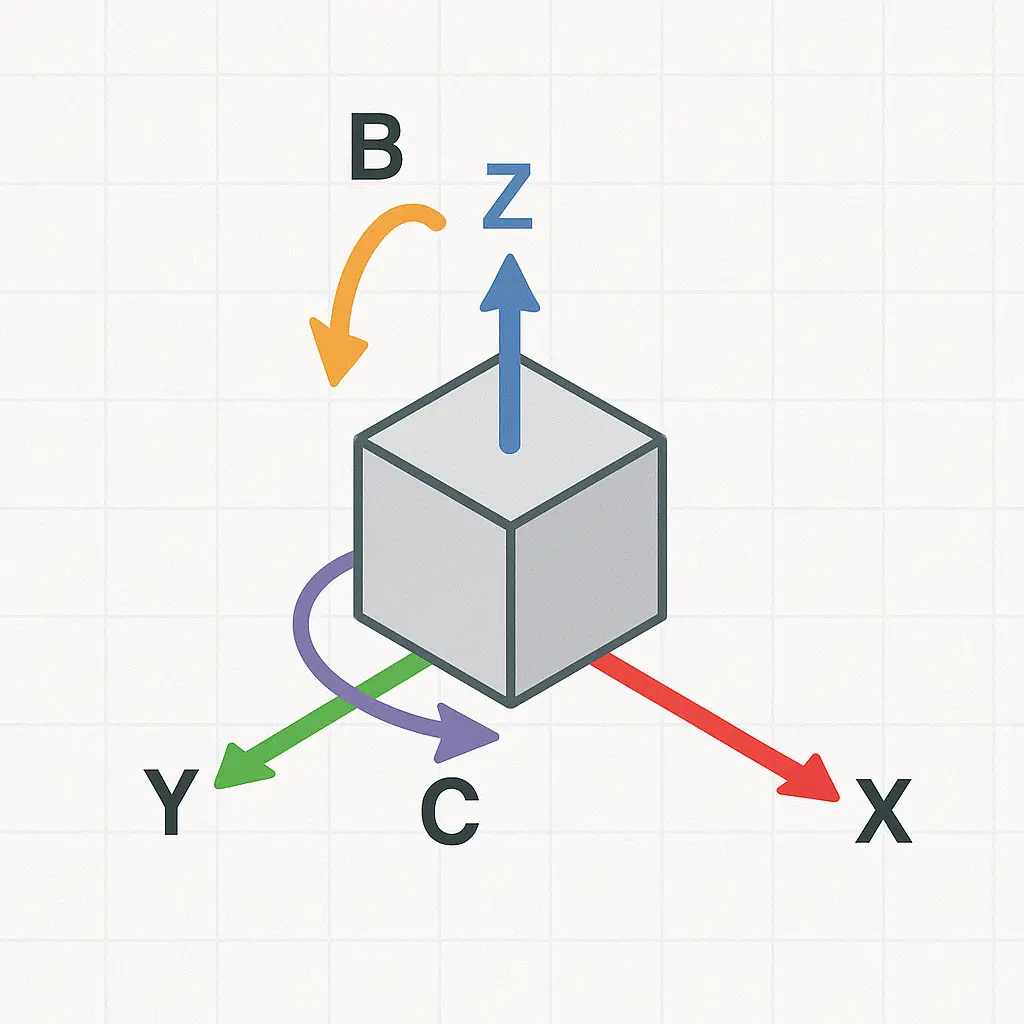
5-Axis Machining
When parts get more complex, our 5-axis machining capabilities step in to handle them with ease. In 5-axis machining, the cutting tool and/or the part can rotate along two additional rotary axes (typically A, B, or C), allowing the tool to approach the part from virtually any angle.
Why 5-Axis:
- Single-Setup Machining: Complex multi-surface parts can often be fully machined without removing and refixturing the part. This greatly reduces human error and improves final accuracy.
- Superior Surface Finish: With optimized tool paths, we minimize tool deflection and create smoother finishes, especially on curved surfaces.
- Complex Geometries: We can easily machine parts with compound angles, undercuts, deep cavities, and features that are inaccessible to standard 3-axis machines.
- Efficiency at Scale: While 5-axis is famous for prototypes and specialty work, it’s also incredibly effective for small-to-medium production runs where complexity would otherwise cause bottlenecks.
Typical 5-Axis Applications:
- Aerospace brackets and housings requiring multi-angle features
- Medical implants and surgical devices with organic contours
- Robotics frames and armatures with intersecting features
- Tooling components with intricate surfaces and undercuts
Our DVF Series (5-axis vertical machining centers) from DN Solutions give us full simultaneous 5-axis control, allowing us to run highly efficient tool paths that reduce cycle times while achieving superior quality.
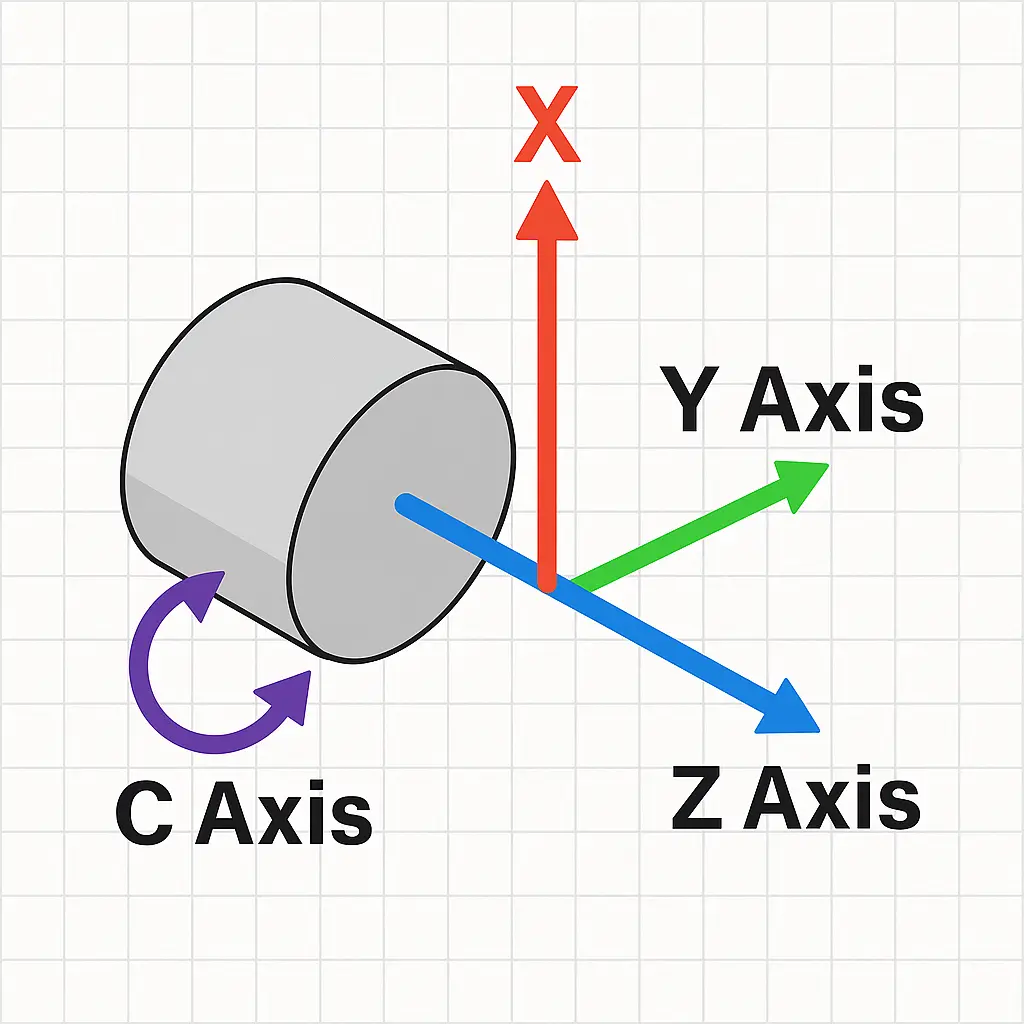
CNC Turning & Mill-Turn Capabilities
When parts require both rotational precision and multi-feature machining, our CNC turning and mill-turn capabilities step in to handle them with efficiency and ease. Using advanced lathes and integrated milling spindles, we produce complex, high-precision parts in a single streamlined process.
Why CNC Turning & Mill-Turn:
Single-Setup Production: Mill-turn machines allow us to perform turning, milling, drilling, and tapping operations in one setup. This greatly reduces manual handling, saves time, and improves dimensional consistency between features.
Superior Surface Finishes: With optimized speeds and feeds for both turning and milling operations, we achieve excellent surface finishes on both cylindrical and flat features—reducing or eliminating the need for secondary finishing.
Complex Features on Turned Parts: We easily produce turned parts with cross-holes, flats, keyways, threads, and milled slots—features that traditionally would require multiple machines or hand setups.
Efficiency at Volume: Mill-turn machining isn't just for prototypes—it’s highly effective for small to large production runs where minimizing operations directly lowers part cost and improves lead times.
Typical CNC Turning & Mill-Turn Applications:
- Hydraulic and pneumatic fittings with internal and external threads
- Shafts and axles with milled flats or drilled cross-holes
- Flanges, adaptors, and precision couplings
- Robotic arm components with turned bodies and milled features
- Valve bodies, manifolds, and connector housings
Our PUMA Series CNC lathes from DN Solutions are equipped with live tooling and sub-spindle capabilities, giving us the flexibility to machine multiple complex features in a single cycle—boosting efficiency while ensuring tight tolerances and superior part quality.
Why Having Both 3-Axis and 5-Axis Matters
By having both 3-axis and 5-axis CNC machining in-house, we offer a flexible, application-driven approach to manufacturing:
Need | Our Solution |
Simple, fast parts | 3-Axis machining for lower cost and rapid turnaround |
Complex, multi-surface parts | 5-Axis machining for tight-tolerance precision |
High-volume production with speed requirements | 5-Axis machining enables high spindle speeds, faster tool paths, and fewer setups |
Prototypes evolving into production | Start with 5-axis flexibility, scale up with optimized setups |
Price-sensitive projects | Strategic use of the right platform for the right geometry |
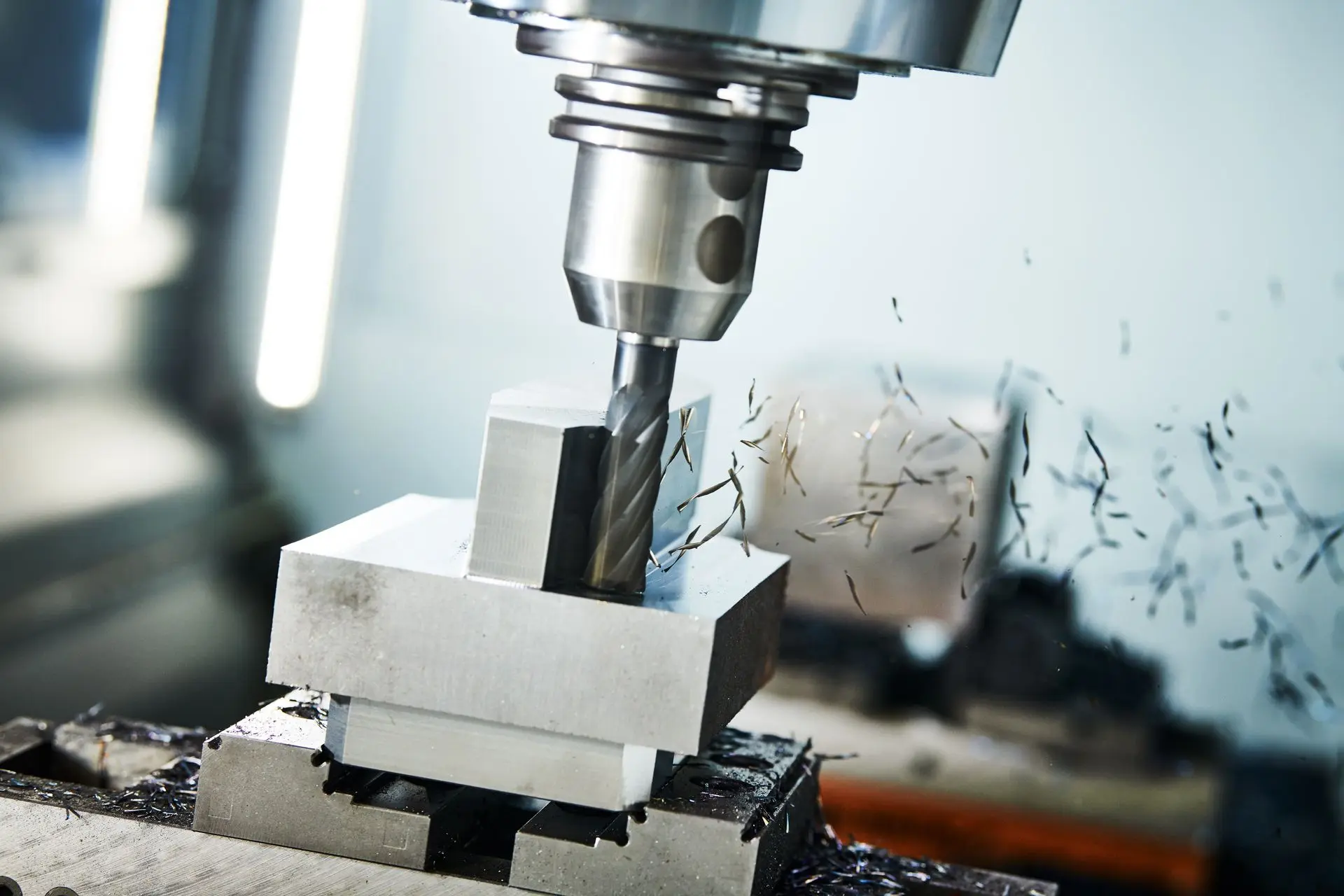
Did You Know?
A complex part requiring four setups on a 3-axis machine can often be completed in a single setup on a 5-axis machine—saving hours of machining time and improving final precision.
Rather than force every project into a one-size-fits-all workflow, we carefully select the most appropriate machining process for your part based on our manufacturing expertise and the specific information you provide through your instant quote request. When you upload your CAD files, technical drawings, and any additional requirements, our experienced team reviews the critical features, tolerances, material specifications, and surface finish needs to determine the best path forward.
Our goal is simple: achieve your desired result with the most efficient, cost-effective, and reliable process possible—while maintaining the highest standards of quality. When a project demands higher volumes and faster turnarounds, 5-axis machining provides a major advantage.
With higher spindle speeds, optimized cutting angles, and the ability to machine more features in fewer setups, 5-axis dramatically reduces cycle time compared to traditional methods. This not only accelerates production but also improves part quality by minimizing manual handling and cumulative errors.
By matching the right technology to the right part, we help you save time, maximize efficiency, and deliver precision parts at scale.
Precision Workholding & Fixturing
Precision work holding is the foundation of our automated machining workflows. We rely on SCHUNK vises and fixturing systems to deliver consistent, repeatable clamping—ensuring that every part is positioned exactly right, every time.
This level of reliability is critical when integrating collaborative robots (cobots) into our operations. Our collaborative robots are programmed to load and unload small parts with large runs with minimal variation, maximizing machine uptime while maintaining tight dimensional tolerances. By combining SCHUNK's world-class clamping technology with robotic automation, we eliminate human variability, speed up production cycles, and achieve truly scalable precision manufacturing.
The result? Faster part throughput, tighter quality control, and the ability to offer competitive lead times without sacrificing craftsmanship.
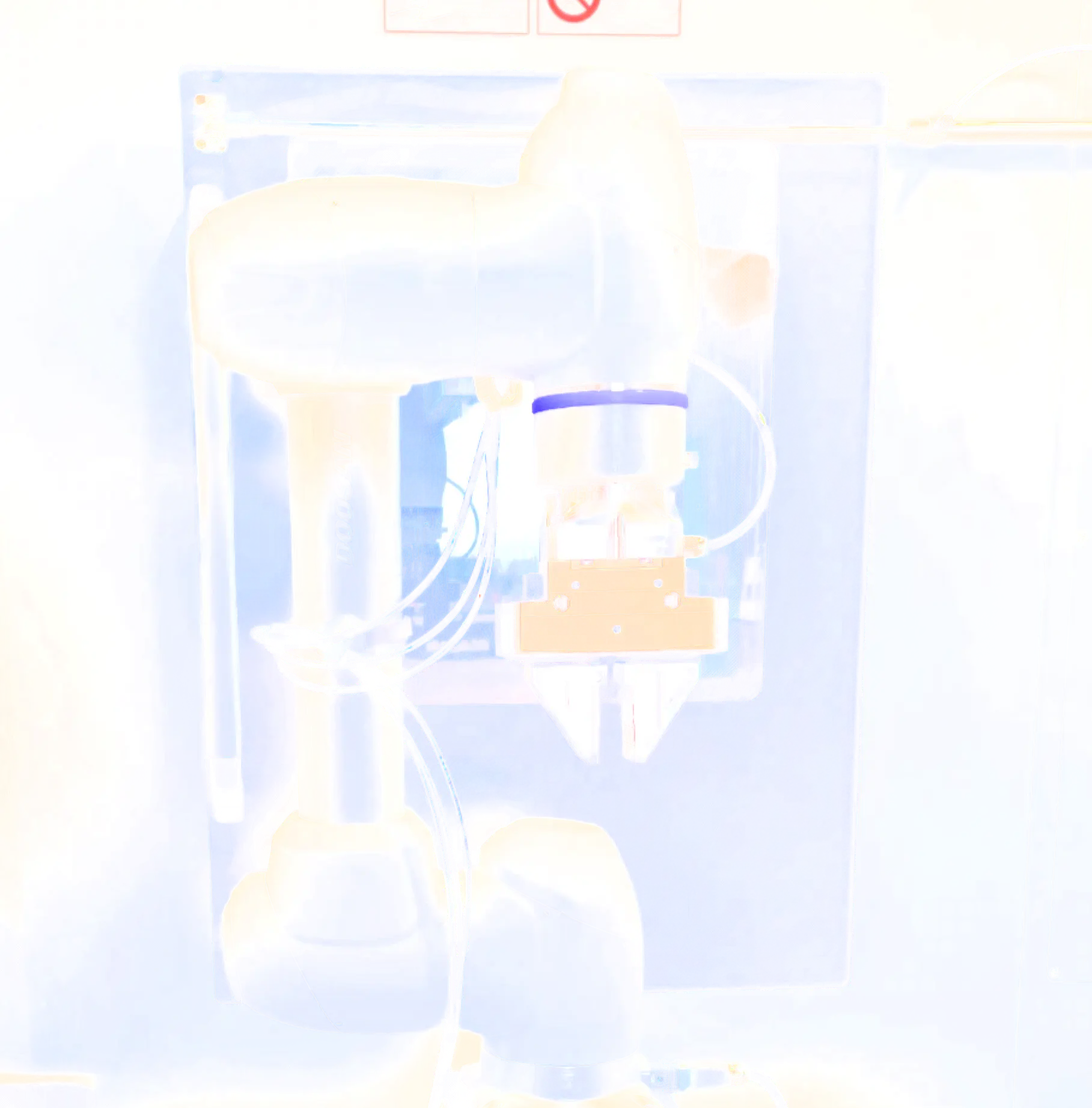
Robotic Automation
To enhance speed and consistency, we’ve integrated collaborative robots (cobots) into our machining workflows. These safe, efficient robotic systems work alongside our operators to automate repetitive tasks like:
- Machine tending – Loading and unloading raw stock or finished parts
- Post-processing – Transferring parts between operations or to quality control
- Lights-out manufacturing – Running machines after hours to increase uptime
As we continue to grow, we are committed to continually updating and adding new technologies to further improve cycle time, accuracy, and volume. Automation helps us keep lead times short, eliminate manual handling errors, and reduce labor costs—while empowering our skilled team to focus on programming, inspection, and complex setups.
By evolving our automation solutions and adopting the latest advancements, we are better positioned to meet the increasing demands of our customers and deliver even greater value.
The Future of Manufacturing Starts Here.
Get your project moving faster with our instant online quoting tool—experience precision and speed like never before.